智慧礦山+智能工廠,海螺集團運用融合工藝機理的信息化技術,推動生產管理模式大變革——
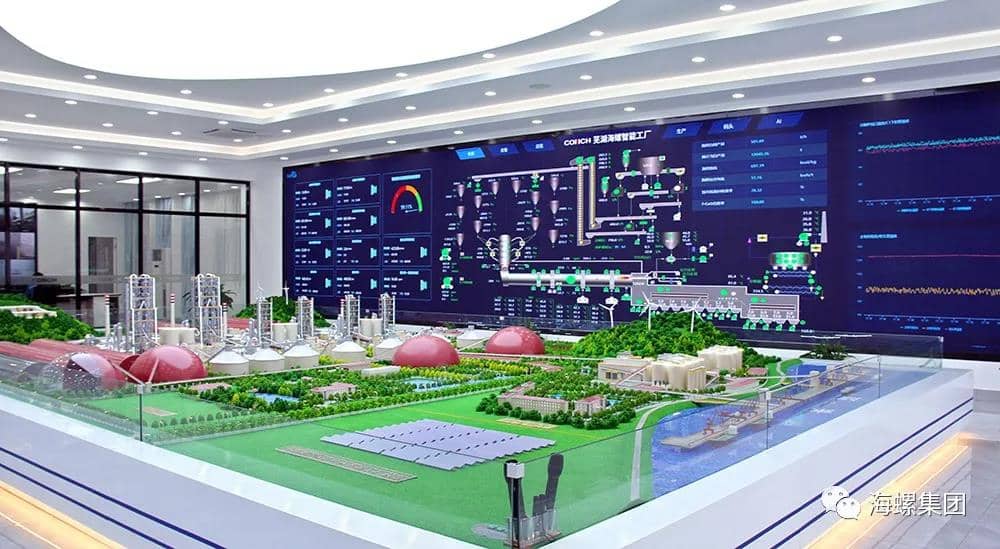
礦山變“綠”
數字化管理系統全面調度,提升資源利用率
“瞧,前面那輛‘巨無霸’就是無人駕駛礦車!”
數字化管理系統全面調度,提升資源利用率
“瞧,前面那輛‘巨無霸’就是無人駕駛礦車!”
4月16日下午,記者跟隨蕪湖海螺水泥有限公司的工作車輛,沿著運礦道路上了礦山。順著身旁工作人員的指引,記者看到一輛有普通轎車三倍“身高” 的綠色礦車正在前方行進。
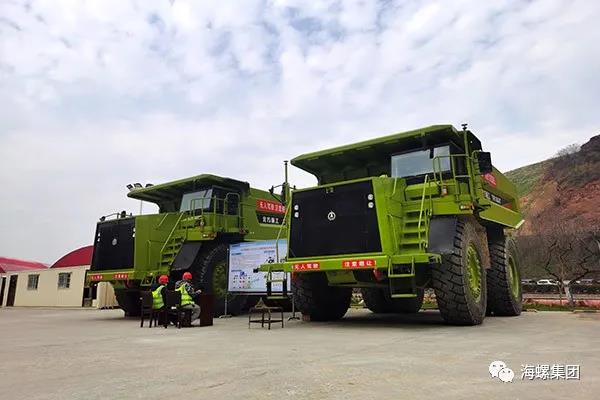
“要實現無人駕駛礦車,不是一件容易的事。”蕪湖海螺礦山分廠副廠長殷亮子說,首先,這需要車輛定位達到厘米級精度,確保礦車在可控范圍內行駛;其次,還要通過建立全局地區、局部地圖以及沿途輔助定位,讓車輛建立感知系統。同時,礦山場景和公路場景的區別很大。礦山是個封閉場景,但環境相對惡劣、車輛工作時間長,因此對系統可靠性要求更高;隨著礦山的開采,也會造成場景不斷變化。目前,蕪湖海螺的無人駕駛礦車仍處于研發階段,礦山上共有4臺無人駕駛礦車在進行測試。“出于安全考慮,礦山內下半夜不作業。今后如果全面實現無人駕駛,礦山就可以進行三班作業,這樣能將采礦效率提高30%。”海螺集團副總經理何承發說。
在蕪湖海螺數字化礦山中央控制室,記者看到大屏幕上分別顯示出礦山各路口實時動態、石灰石在線監測數據等信息。“我們的主要工作是對石灰石進行鏟裝、運輸、破碎,同時還要監測石灰石質量。”殷亮子介紹說,運用數字化礦山管理系統,工作人員可以實現對所有車、鏟、設備的控制和調度。該在哪采礦、運礦道路怎么修建、礦石質量如何把控,都由中央控制室作出決策、發布指令,最終實現各環節有效配合,提升資源利用率,推進綠色礦山建設。
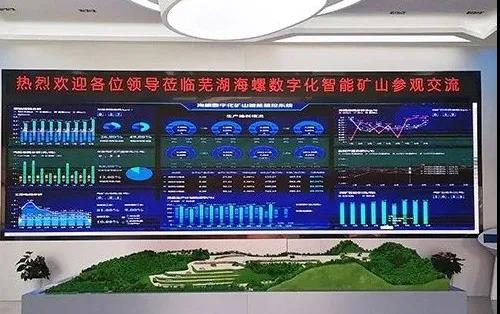
為了讓礦山變“綠”,海螺集團實現了對真實礦山整體數字化再現及各生產要素的智能組合。通過建立礦山三維數字化模型,依據各個部分資源量和品位分布,制定中長期開采計劃,對礦山石灰石進行合理搭配,精準配礦;通過在線質量分析和生產自動配礦、對入堆場石灰石質量實時在線檢測等手段,從源頭上對原料品質進行把控,實現資源利用最大化;通過車輛智能調度,提高礦車利用效率,節省燃油消耗、降低配件消耗。
生產添“智”
“智能工廠”平臺自動引導生產,精準實現節能穩產。一個個小紅點在屏幕上的設備區移動,每個紅點旁邊還顯示了人名……
“這是我們的設備全流程管理系統,掌握著全廠設備運行狀態、設備巡檢等數據。你看到的小紅點,就是員工正在現場開展巡檢,他們手機上都安裝了接入系統的應用程序。”在蕪湖海螺智能工廠中央控制室,工作人員向記者介紹,“如果我們發現設備某個部位出現問題,就發指令給離它最近的員工,員工攜帶儀器進行檢測后,可以將數據實時反饋給系統。”
生產制造執行系統,是2020年上線的“蕪湖海螺智能工廠”模塊之一。隨著工作人員在手機應用程序上點擊、切換,記者面前的大屏幕上又出現了碼頭7個泊位的裝載情況。其中一艘貨船上方標有“熟料”二字,裝載量的數字還在跳動。“這套系統實現了整個生產制造、銷售、發運過程信息化、可視化和智慧化,形成一站式生態服務鏈,從而更加有效地組織生產發運。”工作人員介紹說。
智能質量控制系統,是“蕪湖海螺智能工廠”的另一個模塊。這一系統可通過熟料或水泥的品質預控目標,自動完成在線檢驗、化驗和配料工作。在智能質量實驗室,記者看到一個巨大的機械手臂靜靜佇立,旁邊連接著長長的管道。每隔1個小時,管道內的空氣炮就傳送來各種生料、熟料,由機械手臂直接取樣。“過去我們都要人工取樣。兩年前我剛上班,每次都騎電動車出去取樣,一次取4-6個樣品,大約需要15到20分鐘?,F在有了智能質量控制系統,不僅節約了取樣時間、提高了取樣頻次,還提升了檢驗的精準度,減少人工操作可能出現的誤差。”工作人員俞希凱告訴記者。
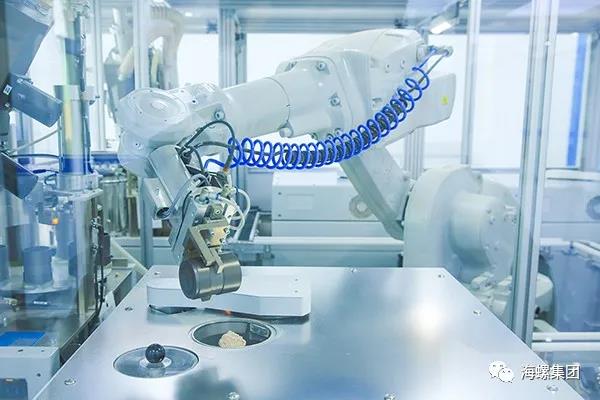
通過“智能工廠”這一平臺, 海螺集團在行業率先實現“一鍵輸入、全程智控”的生產模式,數字化礦山管理系統、智能質量控制系統、專家優化控制系統等模塊各司其職,互相協作。“其中,在生產領域,專家優化控制系統設置好配料參數和品質要求,可在節能穩產模式下自動引導生產,并自動實時采集分析數據,優化生產方案,使產品品質、能源消耗等控制目標不斷逼近預設的最優參數。”何承發說,以水泥行業首個全流程智能化工廠全椒海螺智能質量和優化控制為例,系統能耗下降8%,礦山生產效率提升約12%,操作員勞動強度降低90%以上,人員勞動強度下降24%,檢測頻次提高50%,產品標準偏差降低43%。
融合更“深”
通過業務實現和生態建設路徑,建立工業互聯網平臺
海螺集團智能化建設始于2016年,歷經兩年建成了世界首個水泥全流程智能工廠——全椒海螺;2019年8月,在滁州、蕪湖等地水泥工廠啟動了5G應用探索,完成了全球首個5G“超級上行”創新技術端到端的商業應用,打造了礦車無人駕駛、礦區爆破無人機巡檢、碼頭裝船遠程操控等多個業務應用場景,為工業互聯網建設打下了良好基礎。
當前,我國不斷推進移動互聯網、云計算、大數據、物聯網等新技術與各領域的加速融合,數字化技術與建材行業的深度融合已是大勢所趨。“我們希望通過工業互聯網建設,將企業生產管理經驗軟件化,并進行復制、賦能,促進企業提質增效。”何承發道出海螺集團建立工業互聯網的初衷。
“要想將全椒海螺、蕪湖海螺的應用復制到集團其他工廠,首先要做好各工廠網絡基站的建設和完善。”海螺信息工程公司總經理助理趙波說,“海螺集團在全國25個省市和全球20多個國家都有工廠。目前,我們正在推進這些工廠的網絡建設、升級工作,計劃明年底完成。”同時,海螺集團已啟動“海螺水泥工業大腦”計劃,構建以生產為中心的管理平臺、以財務為中心的經營體系。“這就是我們的‘左腦’‘右腦’,兩者數據共享,進一步提升企業管理效益。”何承發說。
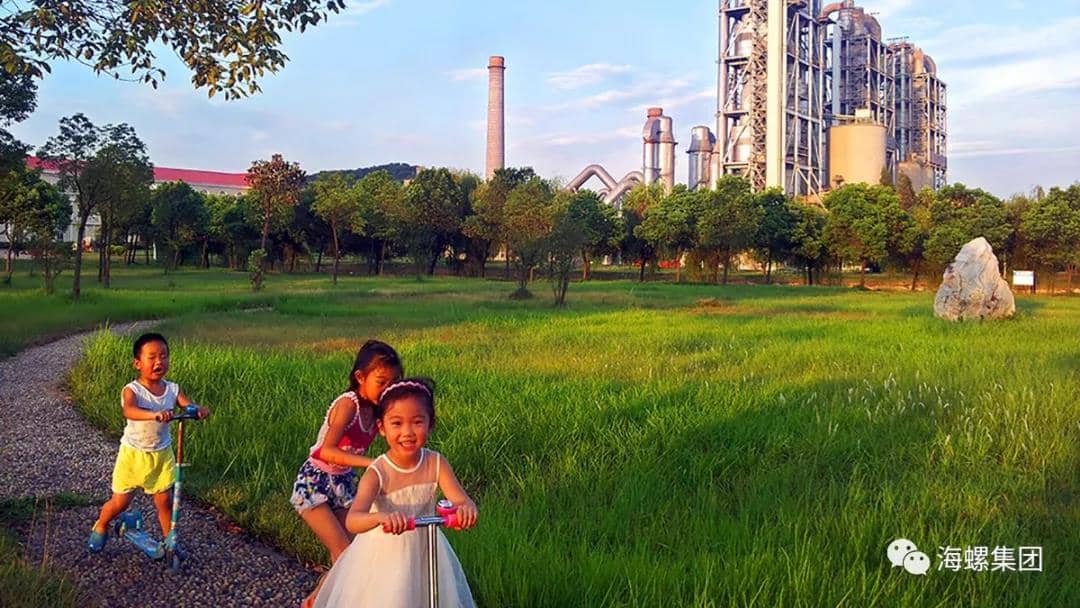
經過前期經驗積累,海螺集團工業互聯網建設路徑逐漸明晰。在業務實現路徑方面,將以“面向生產過程優化的智能制造”“企業運營的管理決策優化”“碳中和技術輸出與指標交易”“供應鏈資源優化配置與商業創新”四個方面作為建設主攻方向,通過構建開放型的工業互聯網體系,逐步將“內需求”擴展到“外需求”,充分挖掘工業互聯網的潛在價值。在生態建設路徑方面,通過“優勢產業引導企業上平臺”“合作吸引區域企業上平臺”“開放和創新吸引開發者上平臺”三種模式,整合產業上下游生態資源,擴大平臺生態圈,形成開發者與工業用戶之間相互促進、雙向迭代的生態體系,為行業內中小企業提供創新服務,為區域內企業提供相對通用的解決方案與服務,促進面向特定領域、特定場景、特定功能的創新型工業應用。
“我們選取了海螺集團的水泥板塊和型材板塊,同步建設面向流程行業的工業互聯網平臺,和面向離散行業的工業互聯網平臺。今年底將初步建成行業級工業互聯網平臺,2022年建成省內具有較強影響力的‘雙跨’平臺。”何承發說。