一、改造背景
日照中聯水泥擁有兩條2*2500t/d新型干法水泥熟料生產線,采用窯外預分解旋窯生產工藝。應環保要求,2014年日照中聯水泥增加SNCR脫硝系統降低NOX排放。使用初期,NOX排放指標為400mg/m³以下,脫硝氨水使用量1#窯約300Kg/h,2#窯約450Kg/h。在2017年NOX排放指標調整為300mg/m³以下,1#窯約430Kg/h,2#窯約650Kg/h,下表是2014年至2018年脫硝氨水消耗統計。
2014年至2018年脫硝氨水消耗統計表
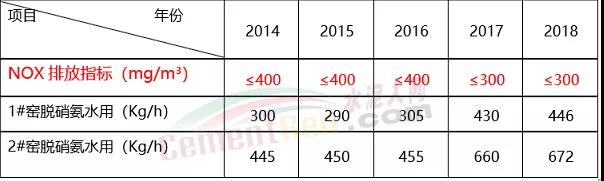
從上表統計可以看出,2017年NOX排放指標調整為≤300mg/m³后,雙窯脫硝氨水使用量明顯升高。其中,1#窯升高140Kg/h,2#窯升高216Kg/h,最高瞬時用量達到1000Kg/h以上,造成生產成本升高的同時帶來較大安全隱患(棗莊某水泥廠2018年發生脫銷氨水閃爆事故,窯門直接飛出近5米遠),并且帶來氨逃逸增加問題。
二、原因分析
熟料煅燒過程中NOX生成原理:燃料燃燒過程中,高溫下由助燃空氣中的N2和O2化合形成。助燃空氣中的氮,在高溫下被氧化,其反應所需要的活性氧原子也來源于氧分子的高溫裂解。
其反應方程式為:N2+O2—→2NO;NO+1/2O2—→NO2
由燃料燃燒生成的NOX占熟料生產生成的的NOX總量的絕大部分。另外原料中含氮氧化物分解形成的NOX,在生成的NOX總量中,其占有比例很小。
因此,在熟料生產過程中,NOX總量的大部分產生于回轉窯的煅燒過程,減少和還原回轉窯產生的NOX是降低脫銷氨水使用量關鍵。因此,利用分解爐錐部還原區對NOX進行還原能有效減少脫硝氨水用量。
2CO+NO2—→2CO2+N2
根據武漢理工大學謝峻林教授團隊的數值模擬技術,日照中聯水泥2#分解爐內氣體流向如下圖:
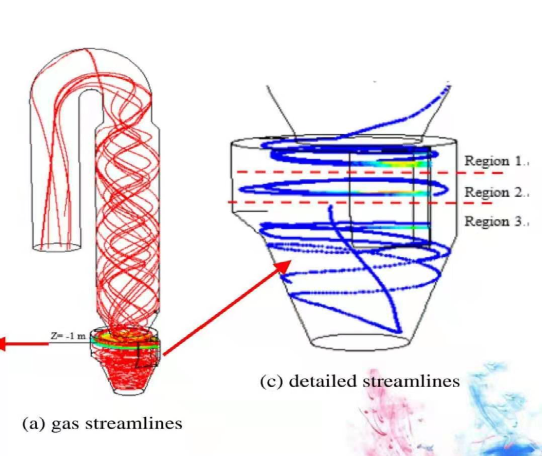
通過上圖,可以清晰的看到三次風進入分解爐錐體后,氣流有向下運動的軌跡,從而導致分解爐設計的還原區實際面積較小,并且三次風帶來充足的O2使得尾煤燃燒較充分,無法產生足夠的還原劑CO,使得2#窯脫硝系統氨水使用量偏高。
三、確定改造方案
結合日照中聯水泥實際情況,經多次分析研究,日照中聯水泥決定先對2#窯三次風管入爐位置進行調整,將原先下傾15°入爐管道改造為接近水平入爐,改變入分解爐三次風方向,增大分解爐錐體還原區體積。同時將原尾煤燃燒器離三次風管較遠的一只位置下移,實現分級燃燒,從而產生足夠的還原劑CO。
施工圖紙如下:
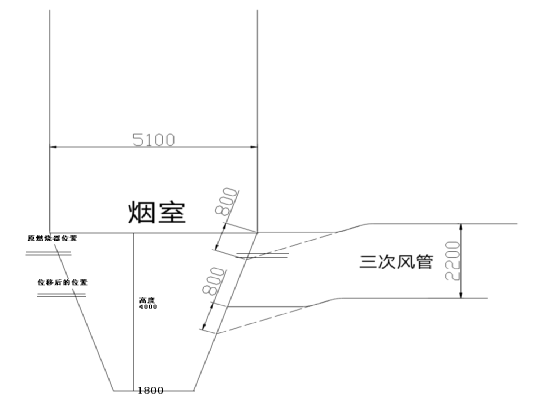
四、改造效果
2018年底,在錯峰停機期間,對2#窯入分解爐三次風管按照既定改造方案實施位移改造。根據計算,改造后分解爐錐體還原區面積從約12m³擴大到約25m³。同時,對回轉窯尾煤燃燒器位置進行調整,從原先尾煤平行對向噴入分解爐,調整為一上一下噴入分解爐,實現分級燃燒。
改造完成后,回轉窯于2019年3月15日恢復生產,至6月1日錯峰停機,2#窯脫硝氨水使用量降至400Kg/h以下,較改造前氨水使用量減少約260Kg/h,改造效果良好。
經濟效益:按全年運行210天,節省氨水使用量按260Kg/h計算,則年可節約氨水使用量210d*24h/d*260Kg/h/1000t/kg=1310t,氨水采購價格按710元/噸,年可節約氨水采購費用1310t*710元/t=93萬元。
2020年,NOX排放指標調整為≤100mg/m³后,2#窯回轉窯脫銷氨水用量在500-550Kg/h,較改造前NOX排放指標≤300mg/m³仍節約120Kg/h,使用效果良好。
五、結束語
通過對2#回轉窯三次風管入分解爐進口角度改造,擴大了還原區面積;通過尾煤燃燒器位置調整改造,實現尾煤分級燃燒,有利于還原劑CO的產生,從而大幅降低了脫銷氨水用量,不但降低了生產成本,還降低了安全風險,減少了氨逃逸造成的二次環境污染。