隨著節能減排要求的逐漸深入,水泥窯尾煙氣性質發生較大改變。現階段,進入窯尾除塵器的煙氣溫度普遍偏低,一般為80-95℃;且隨著氮氧化物排放要求提升,噴氨量加大的情況下,煙氣中氨含量普遍偏高;部分礦石及原料含硫量高的水泥生產線,煙氣中硫含量較高;部分水泥窯新配套協同處置危廢、固廢,使得窯尾煙氣成分更加復雜。如此工況條件下,窯尾除塵器腐蝕問題日益嚴重,已經成為影響窯尾除塵器使用效率和使用壽命的重要因素之一,亟待解決。
1.窯尾除塵器腐蝕及腐蝕介質來源
集中調研窯尾袋除塵器產生腐蝕現象的水泥生產線,發現窯尾煙氣中產生腐蝕的主要介質有NO2、硫氧化物、硫酸氫銨及亞硫酸氫銨、氯離子等。NO2主要來源于燃燒過程中空氣中N2氧化,以及原料中各類基底N元素燃燒氧化;硫氧化物主要來源于燃料燃燒以及礦石煅燒,部分生產線窯尾煙氣中硫含量嚴重超標;硫酸氫銨中的氨來源于氮氧化物治理過程中噴入的氨水和尿素,硫來源于燃料燃燒以及礦石煅燒;氯離子腐蝕主要存在于協同處置固廢、危廢的水泥生產線,固廢、危廢中的鹽分進入煙氣后造成煙氣中氯離子含量過高。
?表1 不同生產線運行狀態

大部分水泥生產線采用SNCR或SCR技術控制氮氧化物排放,硫含量較高的生產線采用濕法或干法脫硫技術來控制硫化物排放。脫硝技術依靠氨水和尿素作為還原劑,存在一定的氨逃逸現象;特別是SNCR技術,一般需要氨氮比達到1.3以上才能起到最佳的氮氧化物減排效果,過高的氨氮比必然造成大量的氨逃逸。含硫量高的煙氣雖然大部分配套了濕法脫硫,但受工藝限制,濕法脫硫位于煙氣治理末端,而采用前段干法脫硫的生產線煙氣中硫含量依舊較高,達到220~900mg/Nm3。過量的氨與二氧化硫可生成亞硫酸氫銨,與三氧化硫可生成硫酸氫銨。
節能減排形式下,目前除塵器入口煙氣溫度普遍較低,使得除塵器內部局部區域,例如人孔門等易漏風區域以及保溫薄弱的區域,易產生凝結水。硫氧化物、硫酸氫銨、亞硫酸氫銨、氯離子等腐蝕介質溶于凝結水后使得凝結液呈酸性,對碳鋼產生化學腐蝕、電化學腐蝕及氧化腐蝕。
新的環保形式下,水泥行業開始采用SCR技術對氮氧化物進行減排,雖然SCR技術采用更少的噴氨量,但目前水泥行業SCR技術使用的釩-鈦系催化劑對SO2向SO3轉化具有一定的催化效果,SO3與氨產生反應后生成腐蝕性更強的硫酸氫銨(硫酸氫銨腐蝕性大于亞硫酸氫銨)。同時,SO3與煙氣中的水蒸氣可生成硫酸蒸汽,并且煙氣的酸露點與SO3含量呈正比關系,SO3含量升高將提高煙氣的酸露點,使得煙氣容易結露形成硫酸溶液。
亞硫酸氫銨和硫酸氫銨溶于凝結液后使得凝結液具有較強的酸性,腐蝕殼體碳鋼。硫酸氫銨在低溫環境下極具吸附性、粘性和吸水性,使得濾袋表面的粉餅層容易板結。板結后的粉餅層極難經壓縮空氣噴吹清理,造成嚴重的“糊袋”現象。部分配套濕法脫硫的水泥生產線選擇將脫硫廢水大量噴入原料磨,原本被濕法脫硫吸收的硫酸氫銨和酸根離子再次返回窯尾煙氣形成富集,使得腐蝕和“糊袋”現象進一步加劇。
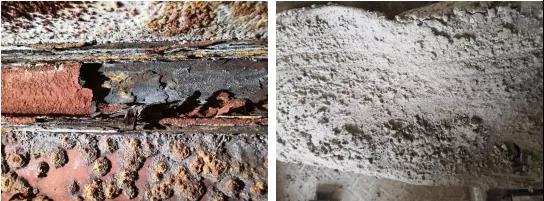
窯尾除塵器腐蝕現象(左)窯尾除塵器“糊袋”現象(右)
低溫條件下(文獻顯示低于108℃),硫酸氫銨和亞硫酸氫銨對碳鋼的腐蝕能力快速增強;在除塵器內部低溫區域,若產生凝結水形成硫酸和亞硫酸的酸性凝結液,除了酸性凝結液本身對碳鋼具有強腐蝕性外,還會加強硫酸氫銨和亞硫酸氫銨對碳鋼的腐蝕能力,形成多物質協同腐蝕,使得腐蝕速率急劇加快。
殼體焊縫區域,由于焊條與殼體基材存在成分差異,焊縫影響區域與基材亦存在成分差異,成分差異會加速電化學腐蝕。板材連接區域及夾角區域,細小縫隙聚集酸性凝結液后,形成“縫隙腐蝕”,加快腐蝕發展速度。現場實地勘察發現,焊縫區域和板材連接區域的腐蝕比其他區域更為嚴重。
2.硫氧化物及NO2腐蝕機理及腐蝕特征
硫氧化物及NO2兩種腐蝕介質中,主要的腐蝕介質為硫氧化物,原因在于SO3可與煙氣中的水蒸氣反應生成硫酸煙霧,在酸露點提高的情況下,易凝結成腐蝕性極強的硫酸溶液。硫氧化物腐蝕機理如下:
硫氧化物腐蝕實際上是稀硫酸的化學腐蝕,其腐蝕特性遵循非氧化性酸的腐蝕規律。化學反應式:Fe+H2SO4=FeSO4+H2↑。硫氧化物腐蝕后產生的FeSO4,在煙氣中SO2和O2的作用下又可生成硫酸鐵:2FeSO4+SO2+O2=Fe2(SO4)3。Fe2(SO4)3附著沉積在壁板上,形成腐蝕產物層。硫酸鐵是一種酸性的、易吸潮的物質。當部分區域溫度降低時,Fe2(SO4)3即開始吸潮潮解,在此區域殼體表面形成強酸性的腐蝕環境。如果停窯時腐蝕產物沒有及時清除,那么在整個停窯階段原來的腐蝕區域將一直受到稀酸腐蝕的侵害。即Fe2(SO4)3本身也將對金屬腐蝕生成FeSO4。從而形成FeSO4→Fe2(SO4)3→FeSO4 的腐蝕循環,大大加快了腐蝕的進程。此外,硫氧化物還會產生電化學腐蝕,其機理見硫酸氫銨腐蝕機理。
硫氧化物腐蝕外觀表象為腐蝕區域成片分布且較均勻,附著層狀、塊狀松散腐蝕產物,顏色多為棕褐色及黑色。
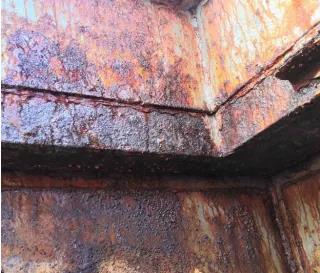
3.硫酸氫銨腐蝕機理及腐蝕特征
殼體局部區域產生冷凝液,煙氣中亞硫酸氫銨和硫酸氫銨溶于其中使得冷凝液呈較強酸性,酸性冷凝液中H+得電子析出氫氣,這種電化學腐蝕稱為析氫腐蝕,其反應方程式為:
負極:Fe-2e-→Fe2+
正極:2H++2e-→H2↑
總反應:Fe+2H+→Fe2++H2↑
隨著氫氣的析出,冷凝液的pH值上升,當上升至呈弱酸性或中性時,冷凝液能溶解較多氧氣,此時O2得電子而析出OH-,這種電化學腐蝕稱為吸氧腐蝕,是造成碳鋼腐蝕的主要原因。漏風區域煙氣氧氣含量比其他區域高,使得此區域腐蝕比其他區域更為嚴重。吸氧腐蝕反應方程式為:
負極:Fe-2e-→Fe2+
正極:2H2O+O2+4e-→4OH-
總反應:2Fe+O2+2H2O→2Fe(OH)2
Fe(OH)2會被O2進一步氧化生成Fe(OH)3,Fe(OH)3脫去一部分水生成Fe2O3·nH2O,即鐵銹的主要成分。
硫酸氫銨具有較強的吸附性、粘性和吸濕性,附著在殼體壁板表面后吸附粉塵、水分以及更多的腐蝕物質,使得附著點腐蝕加速,形成大量腐蝕產物。硫酸氫銨腐蝕典型的特征為腐蝕產物形成密集腐蝕堆,外觀表象多為暗黃色及灰黃色,且周圍分布有白色結晶鹽。
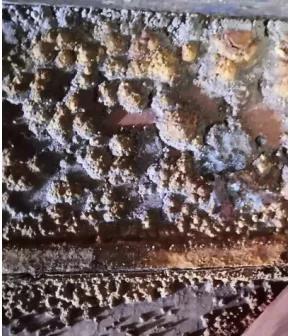
4.氯離子腐蝕機理及腐蝕特征
酸性凝結液環境下,各類腐蝕介質中,Cl-具有離子半徑小、穿透能力強的特點,并且易被金屬表面吸附,使得其極易穿透碳鋼表面氧化層和保護層,對殼體腐蝕的影響最大。凝結液中Cl-濃度越高,凝結液的導電性就越強,凝結液電解質的電阻就越低,煙氣中Cl-溶于凝結液后就越容易到達金屬表面,加快局部腐蝕的進程。腐蝕過程中,Cl-會在有凝結液的區域處富積,Cl-積聚成核后,形成電化學腐蝕,使得該區域陽極溶解加速,碳鋼基體被向下深層腐蝕,形成點蝕坑。陽極金屬的溶解,會加速Cl-透過腐蝕產物擴散到點蝕坑內,使點蝕坑內的Cl-濃度進一步增加和富集,加快腐蝕速率,這一過程也稱為Cl-的催化機制。當凝結液中Cl-濃度超過一定的臨界值之后,陽極金屬將一直處在活化狀態而不會被鈍化。因此,在Cl-的催化作用下,點蝕坑會不斷擴大、加深,嚴重時甚至會造成殼體穿孔。
在殼體金屬表面產生大量點蝕坑,是氯離子腐蝕最主要的腐蝕特征。殼體應力集中的區域,Cl-的存在還會加速應力腐蝕的發展,使得殼體基材快速斷裂失效。夾角等細小縫隙區域,Cl-會加速縫隙腐蝕,快速破壞殼體基材。
氯離子腐蝕(除銹后)
5.腐蝕防護措施
窯尾除塵器腐蝕及糊袋問題嚴重影響設備使用率和使用壽命,各生產企業和設計單位均投入了一定的資源研究解決措施,現階段常見的處理措施如下。
調整操作工藝,平衡各工藝段最佳運行參數,控制除塵器入口溫度在110℃以上,防止低溫結露。合理配料,減少停磨時間,增加窯尾煙氣經過生料磨的時間,降低煙氣中硫含量。采用新的煙氣治理技術,降低煙氣中腐蝕介質的含量,從根本上降低進入窯尾除塵器的腐蝕介質含量。
停窯后除塵器脈沖閥繼續噴吹,將濾袋上聚集的粉塵清理干凈;同時窯尾風機繼續運行,將系統中殘余的煙氣抽取干凈,減少腐蝕介質聚集,防治冷空氣進入后造成“糊袋”現象,以及加劇殼體腐蝕。
改變除塵器殼體結構,例如將頂開蓋結構改造為大凈氣室結構,減少蓋板、人孔門等漏風點的數量;改進焊接工藝,加強除塵器殼體密封性,改進人孔門結構,減少漏風率及漏風點,減少冷空氣進入量。采用整體密閉防雨棚,增強外保溫的保溫性能,降低外露面溫降,避免過大的系統溫差;改善壓縮空氣性能,降低其含水率,有必要的情況下,利用煙氣余熱對壓縮空氣進行預熱,避免噴吹時個別區域產生急劇溫差。
當前針對窯尾除塵器腐蝕采用的防腐涂料有環氧富鋅漆、有機硅漆、聚氨酯漆、玻璃鱗片涂料、石墨烯涂料等;采用的物理隔離措施有陶瓷貼片、惰性物質貼片等。
其中環氧富鋅漆的防腐原理為利用鋅元素替代碳鋼組成陰極保護,但在電化學腐蝕的作用下,漆中的鋅元素很快被腐蝕消耗完,使得漆的保護作用失效,因此每個檢修周期必須重新涂刷,防腐效果不佳。其他種類防腐涂料和物理隔離措施在較高要求的施工條件下,均具有一定的防腐效果。
不少配制了濕法脫硫的水泥生產線選擇將極難處理的脫硫廢水噴入原料磨,此舉會造成窯尾煙氣中腐蝕介質形成富集,加劇窯尾除塵器腐蝕。可采用“脫硫廢水篦冷機煙道蒸發技術”對脫硫廢水進行零排放治理[5],降低窯尾煙氣中腐蝕介質的來源。
鳳陽某廠、漳平某廠窯尾除塵器采用涂刷環氧富鋅底漆作為防腐措施,運行約三個月內防腐效果良好。但后期環氧富鋅漆中鋅元素消耗完畢,除塵器產生嚴重腐蝕現象。
千陽某廠、北流某廠窯尾除塵器部分區域腐蝕嚴重,停窯檢修時對過煙氣面進行除銹打磨處理,整體涂刷醇酸防銹底漆,然后整體涂刷聚氨酯面漆。半年后檢查發現,除個別漏風嚴重區域、焊縫及夾角區域以外,其他區域具有一定的防腐效果。

昆明某廠新建線窯尾除塵器采用噴涂水泥砂漿的形式進行防腐,運行半年后未發現腐蝕現象。但水泥砂漿層影響檢修后二次安裝,且容易脫落,脫落后產生的細小顆粒物影響排放數據。
海螺水泥某基地窯尾除塵器采用TD103# 耐石墨烯防腐涂料,半年后檢修檢查發現防腐效果尚可。但此措施施工條件苛刻,需要較高精度的噴砂打磨等級,且費用昂貴。
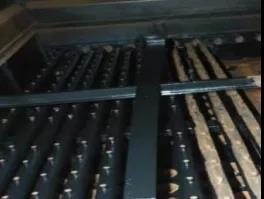
禮泉某廠采用防腐陶瓷貼片作為窯尾除塵器防腐措施,使用三個月后發現具有一定的防腐效果。但貼片安裝粘貼時采用特殊膠水粘接,且貼片和貼片之間亦有膠水縫隙,膠水被腐蝕介質腐蝕破壞后容易造成陶瓷貼片脫落,貼片之間的縫隙存亦在腐蝕現象。同時,此措施費用較為昂貴。
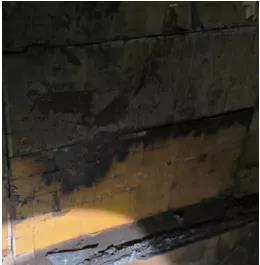
6.進一步研究工作
(1)收集產生腐蝕現象的典型水泥生產線的運行數據,對比分析脫硫脫硝系統投產前后工況參數變化,辨別產生腐蝕現象的前后不同原因。
(2)對比分析不同水泥生產線腐蝕介質的差異化,取樣化驗煙氣成分及粉塵組分,分析腐蝕物質含量的差異,尋找不同工藝條件下造成窯尾袋除塵器腐蝕的不同主要腐蝕介質。
(3)針對不同主要腐蝕介質造成的窯尾除塵器腐蝕,有針對性采取防腐措施,例如配制不同組分的特殊防腐涂料或采取其他物理隔離措施。
7.總結
當前,水泥窯尾除塵器腐蝕問題已經成為普遍現象,嚴重影響窯尾除塵器穩定運行和使用壽命。窯尾煙氣中主要腐蝕介質有硫氧化物、硫酸氫銨及亞硫酸氫銨、氯離子等,并且產生腐蝕的主要條件之一為局部低溫環境形成酸性凝結液。局部低溫環境下,窯尾煙氣中的腐蝕介質對殼體碳鋼產生硫氧化物腐蝕、亞硫酸氫銨及硫酸氫銨腐蝕、氯離子腐蝕等典型腐蝕問題,同時亞硫酸氫銨及硫酸氫銨還容易造成窯尾袋除塵器“糊袋”現象。
可通過改進水泥窯操作工藝、改進除塵器結構、涂刷防腐涂料及采用物理隔離、對脫硫廢水進行零排放處理等措施來預防和治理窯尾除塵器腐蝕問題。后期可展開進一步研究工作,針對不同現場因素,辨別不同工藝條件下造成窯尾袋除塵器腐蝕的不同根本原因,以便采取合理針對措施解決窯尾除塵器腐蝕問題。
參觀考察可聯系:
張總 18910037609
雷總 13379201775